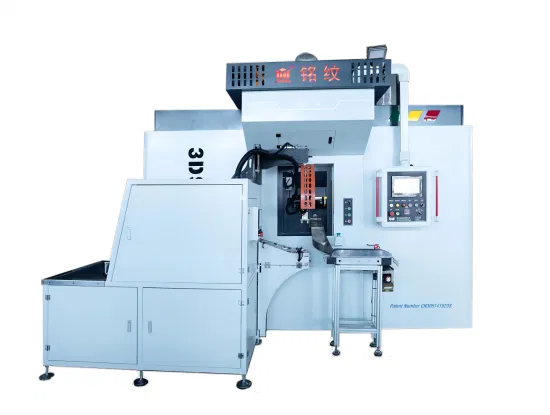
Vertikale Rotationstransfermaschine zum Gießen von selbstschließenden Ventilen aus Aluminium
Übersicht Produktbeschreibung Parameter: Multi-Stationen, Multi-Spindeln-Rotationstransfermaschine (angepasst an spezifi
Senden Sie Ihre AnfrageBESCHREIBUNG
OverviewBasisinformation.
Modell Nr. | 3DSF 9-12 SPS |
Präzision | Präzision |
Zertifizierung | GS, CE |
Zustand | Neu |
Sicherheitsvorrichtungen | mit umfassenden Sicherheitsfunktionen |
After-Sales-Support und Service | Verfügbar |
Qualitätskontrolle | Sorgen Sie für gleichbleibende Qualität |
Maschinengröße und Gewicht | Kompakte Stellfläche |
Verpackung und Transport | Seetauglicher Transport |
Kontrollsystem | CNC |
Original | China |
Marke | MW |
Flexibilität | Hängt vom spezifischen Werkstück ab |
Genauigkeit | Hohe Präzision |
Stationen | Mehrere Stationen individuell angepasst |
Spindeln | Angepasst an das Werkstück |
Kapazität | Massenproduktion |
Transportpaket | Seetaugliche Verpackung |
Warenzeichen | MW |
Herkunft | China |
HS-Code | 8457101000 |
Produktbeschreibung
Produktbeschreibung
Parameter:
Maschinenname | Vertikale Rotationstransfermaschine zum Gießen von selbstschließenden Ventilen aus Aluminium |
Anwendung | Für selbstschließendes Ventil aus Aluminiumguss |
Strukturstil | Vertikal |
Station und Spindel | Station und Spindel – maßgeschneidert auf das jeweilige Werkstück |
Präzision in der Verarbeitung | 0,01 ~ 0,02 (mm) |
Größe und Gewicht der Ausrüstung | Die Größe hängt von den jeweiligen Produkten ab. Gewicht: 6–9 Tonnen (nur als Referenz) |
Zykluszeit: | |
Kontrollsystem | SPS |
Motor der Antriebseinheit | Servomotor |
Fütterungsmethode | Manuell/Automatisch (optional) |
Maßgeschneidert | Auf die spezifischen Werkstücke zugeschnittene Stationen und Spindeln |
Zertifizierung | GS, CE |
Multi-Stationen, Multi-Spindeln-Rotationstransfermaschine (angepasst an spezifische Werkstücke)
Laden/Entladen von Werkstücken (automatisch oder manuell – optional)
Unsere Vorteile
Rundtaktmaschinen bieten aufgrund ihres einzigartigen Designs und ihrer Fähigkeiten mehrere Vorteile in der Fertigungsindustrie. Hier sind einige der wichtigsten Vorteile des Einsatzes von Rundtaktmaschinen:
Hohe Produktionsraten: Rundtaktmaschinen sind für die gleichzeitige Bearbeitung mehrerer Arbeitsstationen ausgelegt und ermöglichen so die gleichzeitige Bearbeitung mehrerer Teile. Dies führt zu hohen Produktionsraten und einem erhöhten Durchsatz, was sie ideal für die Massenfertigung macht.
Präzision und Genauigkeit: Diese Maschinen sind mit hochwertigen Komponenten und fortschrittlichen Steuerungssystemen ausgestattet und gewährleisten eine präzise und genaue Bearbeitung. Die Drehbewegung ermöglicht eine konsistente und wiederholbare Positionierung, was zu engen Toleranzen und einer verbesserten Teilequalität führt.
Reduzierte Rüstzeit: Rundtaktmaschinen sind für den schnellen Wechsel zwischen verschiedenen Produktionsläufen konzipiert. Sobald die Ersteinrichtung abgeschlossen ist, erfolgen nachfolgende Umstellungen relativ schnell, wodurch Ausfallzeiten reduziert und die Gesamteffizienz gesteigert werden.
Flexibilität: Trotz ihrer Kapazität für große Stückzahlen können Rundtaktmaschinen ein breites Spektrum an Teilegrößen und -geometrien verarbeiten. Da sie mehrere Werkzeuge und Vorgänge aufnehmen können, bieten sie Vielseitigkeit bei der Herstellung verschiedener Komponenten.
Kosteneffizienz: Während Rundtaktmaschinen eine erhebliche Anfangsinvestition erfordern, können ihre hohen Produktionsraten und ihre Effizienz auf lange Sicht zu erheblichen Kosteneinsparungen führen. Die reduzierten Arbeitskosten und die höhere Produktion tragen zu niedrigeren Kosten pro Teil bei.
Bedienersicherheit: Rundtaktmaschinen sind oft vollständig geschlossen, um Bediener vor potenziellen Gefahren im Zusammenhang mit dem Bearbeitungsprozess zu schützen. Dieses Gehäuse trägt auch dazu bei, Späne und Kühlmittel einzudämmen, wodurch die Arbeitsumgebung sauberer und sicherer wird.
Minimierte Zykluszeiten: Durch die gleichzeitige Bearbeitung mehrerer Teile und Vorgänge können Rundtaktmaschinen die Zykluszeiten deutlich verkürzen und so die Gesamtproduktivität steigern.
Automatisierungsintegration: Rundtaktmaschinen können problemlos in automatisierte Produktionslinien integriert werden, was deren Effizienz weiter steigert und den Bedarf an manuellen Eingriffen reduziert. Dies ermöglicht eine „Lights-out“-Fertigung, bei der die Maschinen über längere Zeiträume autonom arbeiten können.
Platzsparend: Rotationstransfermaschinen sind so konzipiert, dass sie im Vergleich zu herkömmlichen Fertigungseinrichtungen mit mehreren Einzelmaschinen eine relativ kleine Stellfläche einnehmen. Dieses platzsparende Design trägt zur Optimierung der Stellfläche in der Fabrik bei.
Konsistenz und Zuverlässigkeit: Sobald Rotationstransfermaschinen richtig eingerichtet sind, arbeiten sie in der Regel konstant und zuverlässig, wodurch Schwankungen in der Teilequalität minimiert und das Risiko von Defekten oder Fehlern verringert werden.
Arbeitsprozess
Überblick über die Funktion und den Betrieb einer vertikalen Rundtaktmaschine: Werkstückbeladung: Robort, Manipulator vorhanden Indexierung und Werkstückpositionierung: Der Indexierungsmechanismus der Maschine dreht den Rundtisch und bewegt das Werkstück zu verschiedenen Bearbeitungsstationen, die vertikal um die Achse angeordnet sind. Jede Station ist mit den notwendigen Werkzeugen, Vorrichtungen und Geräten für bestimmte Vorgänge ausgestattet. Bearbeitungsvorgänge: Während das Werkstück zu jeder Station weiterbewegt wird, werden verschiedene Bearbeitungsvorgänge durchgeführt. Diese Vorgänge können Bohren, Fräsen, Gewindeschneiden, Reiben, Bohren, Schleifen, Drehen, Honen oder andere Prozesse umfassen, die für das jeweilige herzustellende Teil erforderlich sind. Spanmanagement: Ähnlich wie andere Arten von Bearbeitungszentren verfügen auch vertikale Rundtaktmaschinen über Spanmanagementsysteme um bei der Bearbeitung entstehende Späne oder Späne zu entfernen. Späneförderer, Späneauffangwannen oder andere Methoden werden eingesetzt, um eine saubere und effiziente Arbeitsumgebung aufrechtzuerhalten. Inspektionen, Messungen oder automatisierte Messsysteme sind in die Maschine integriert. Entladen des Werkstücks: Sobald alle erforderlichen Vorgänge abgeschlossen sind, wird das fertige Werkstück entladen von der Maschine. Der Indexierungsmechanismus bringt den Drehtisch oder die Trommel in die ursprüngliche Ladeposition zurück und der Zyklus kann mit einem neuen Werkstück wiederholt werden
Zertifizierungen
Unternehmensprofil
OEM/ODM
Unser Unternehmen verfügt über ein eigenes einzigartiges Team von Designern für verschiedene Typen, je nach Bedarf der OEM- und ODM-Kunden!
Wir verfügen über mehr als 10 Jahre Erfahrung im OEM/ODM-Service, einschließlich der Entwicklung bestimmter Produktfunktionen, bestimmter Pakete, Musterentwicklung usw.
Forschung und Entwicklung
Unser Unternehmen hat die Abteilung für F&E-Software und die Abteilung für F&E-Maschinen eingerichtet.
Wir haben ein starkes Forschungs- und Entwicklungsteam aus Deutschland, Japan und China.
Auf Ihren speziellen Wunsch hin könnten wir für Sie die Konstruktion einer neuen Maschine mit einer einzigartigen Software und einem Gehäuse Ihrer Basis übernehmen.
Kundendienst
Für die meisten unserer Produkte, wie z. B. CNC-Drehmaschinen, ist technischer Online-Support über soziale Software verfügbar. Eine andere Möglichkeit besteht darin, Module zur Fernüberwachung des technischen Supports in den Geräten vorzuinstallieren, sodass im Falle eines Ausfalls, beispielsweise einer Rundtaktmaschine, technischer Fernsupport über das Internet bereitgestellt werden kann. Für die meisten unserer Maschinen senden wir Ersatzteile für einige der leicht zerbrechlichen Teile mit der Maschine.
FAQ
Wie wird die Maschine gewartet? 1. Wartungsbeauftragter
a) Der Betreiber ist für die Nutzung, Wartung und Grundinstandhaltung der Geräte verantwortlich.
b) Das Wartungspersonal der Ausrüstung ist für die Reparatur und notwendige Wartung der Ausrüstung verantwortlich.
2. Grundvoraussetzungen für die Nutzung von Geräten
a) Bei CNC-Geräten müssen Orte mit Feuchtigkeit, übermäßigem Staub und korrosiven Gasen vermieden werden.
b) Vermeiden Sie direkte Sonneneinstrahlung und andere Wärmestrahlung und halten Sie Präzisionsgeräte von Geräten mit starken Vibrationen fern, wie z. B. Stanzmaschinen und Schmiedegeräten.
c) Die Betriebstemperatur des Geräts sollte zwischen 15 und 35 Grad liegen. Die Temperatur während der Präzisionsbearbeitung sollte bei etwa 20 Grad kontrolliert werden, wobei die Temperaturschwankungen streng kontrolliert werden müssen.
d) Um große Schwankungen der Stromversorgung (±10 %) und mögliche sofortige Störsignale und andere Effekte zu vermeiden, verwenden Geräte im Allgemeinen eine eigene Netzstromversorgung (z. B. aus dem Niederspannungsverteilerraum, um einen separaten Weg für Werkzeugmaschinen aufzuteilen). Zusätzliche Spannungsregler usw. können die Auswirkungen auf die Qualität der Stromversorgung und elektrische Störungen verringern.
3.Tägliche Aufrechterhaltung der Bearbeitungsgenauigkeit
a) Nach dem Einschalten muss die Maschine vor der Verarbeitung ca. 10 Minuten vorgeheizt werden; Bei Maschinen, die längere Zeit nicht genutzt werden, sollte die Vorheizzeit verlängert werden.
b) Prüfen, ob der Ölkreislauf frei ist.
c) Halten Sie die Maschine trocken und sauber.
4.Tägliche Wartung
a) Tägliche Reinigung von Maschinenstaub und -spänen: einschließlich Maschinenbedienfeld, Spindelkegelloch, Werkzeugschlitten, Werkzeugmagazin, Werkzeugarm und Werkzeugbehälter, Revolverkopf, flexibler Schlauch in der Maschine usw.
b) Überprüfen des Schmierölstands, um die Schmierung der Maschine sicherzustellen.
c) Prüfen Sie, ob ausreichend Kühlmittel im Kühlmitteltank vorhanden ist. Füllen Sie die Zeit nach, wenn das Kühlmittel nicht ausreicht.
d) Überprüfen Sie, ob der Luftdruck normal ist.
e) Überprüfen Sie alle Signalleuchten, die Alarmwarnleuchten sind normal.
f) Überprüfen Sie die Leitung der Öldruckeinheit auf Undichtigkeiten.
g) Reinigung der Maschine nach der täglichen Arbeit.
h) Sorgen Sie für eine saubere Umgebung rund um die Maschine.
5. Wöchentliche Wartung
a) Reinigung von Luftsieben von Wärmetauschern, Kühlpumpen, Schmierölpumpensieben.
b) Überprüfen Sie, ob die Werkzeugschraube locker und der Werkzeuggriff sauber ist.
c) Prüfen Sie, ob der mechanische Ursprung versetzt ist.
d) Wenn ein Ölkühler vorhanden ist, überprüfen Sie das Öl des Ölkühlers, z. B. unterhalb der Skalenlinie. Bitte füllen Sie das Öl des Ölkühlers rechtzeitig nach.
e) Reinigen Sie das komprimierte Gas von Verunreinigungen und Wasser, prüfen Sie das Ölvolumen im Ölnebelabscheider, prüfen Sie, ob das Magnetventil jedes Kreises normal funktioniert, prüfen Sie die Abdichtung im Pneumatiksystem und den Zustand des Luftkreissystems wirkt sich direkt auf das Messerwechsel- und Schmiersystem aus.
f) Verhindern Sie, dass Staub und Schmutz in das Innere des CNC-Geräts gelangen. In der Luft des Maschinenraums befinden sich im Allgemeinen Ölnebel, Staub und sogar Metallpulver. Sobald sie auf die Leiterplatte oder elektronische Geräte im CNC-System fallen, kann es leicht zu einem Abfall des Isolationswiderstands zwischen den Elementen kommen, und zwar sogar kann zu Schäden an Bauteilen und Platinen führen.
6. Monatliche Wartung
a) Überprüfen Sie die Schmierung der Wellenlaufbahn. Die Laufbahnoberfläche muss eine gute Schmierung gewährleisten.
b) Endschalter prüfen und reinigen.
c) Überprüfen Sie, ob die Hinweis- und Warnschilder an der Maschine klar sind.
7. Halbjährliche Wartung
a) Entfernen Sie den Späneschutz der Welle, reinigen Sie die Verbindung der Wellenölleitung, die Kugelumlaufspindel und den Endschalter und prüfen Sie, ob sie normal sind.
b) Überprüfen Sie, ob der Servomotor jeder Spindel normal läuft und ob ungewöhnliche Geräusche zu hören sind.
c) Ersetzen Sie das Öl der Hydraulikeinheit und des Untersetzungsmechanismus des Werkzeugmagazins.
d) Entfernen Sie den Staub im Schaltkasten (stellen Sie sicher, dass die Maschine ausgeschaltet ist).
e) Überprüfen Sie vollständig, ob alle Kontakte, Anschlüsse, Buchsen und Schalter normal sind.
f) Überprüfen Sie, ob alle Tasten normal sind.
g) Überprüfen Sie die mechanische Wasserwaage und stellen Sie sie ein.
h) Reinigen Sie den Schneidwassertank und ersetzen Sie die Schneidflüssigkeit.
8. Jährliche professionelle Wartung oder Reparatur
a) Professionelle Wartungs- oder Reparaturarbeiten sollten von professionellen Ingenieuren durchgeführt werden. Bitten Sie Ihren Händler um Hilfe.